What You Should Know About Manufacturing Training
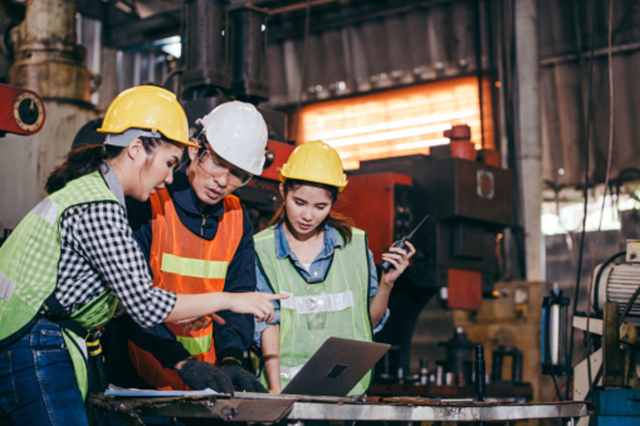
February 9, 2022
Benefits of manufacturing training Training is never excessive, especially in a technical and hard-skills-required industry like manufacturing. Rapid Enterprises and Roundtable Learning, two experts in the manufacturing industry, highly recommended manufacturing training for these reasons: 1. Safety The first benefit of employee training is fundamental level safety. Manufacturing training guarantees that employees understand how to […]
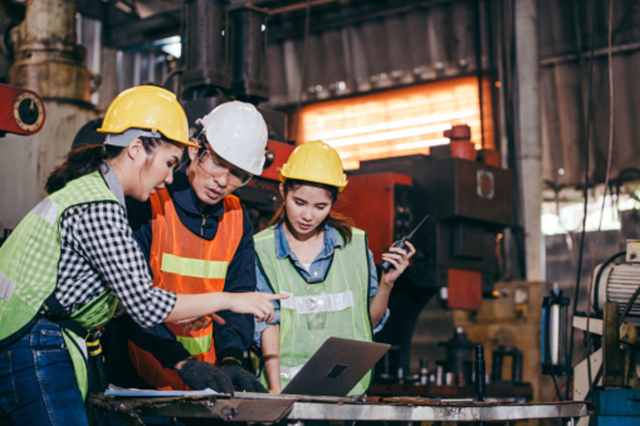
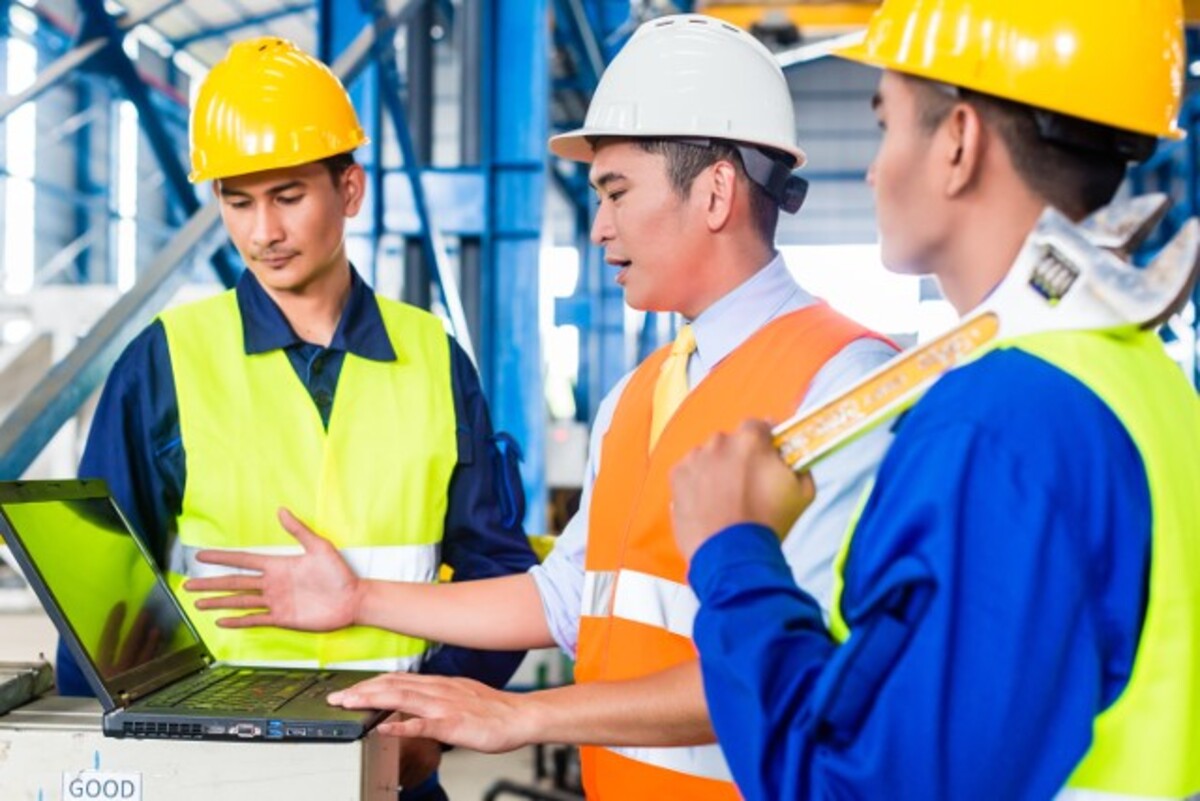
Benefits of manufacturing training
Training is never excessive, especially in a technical and hard-skills-required industry like manufacturing. Rapid Enterprises and Roundtable Learning, two experts in the manufacturing industry, highly recommended manufacturing training for these reasons:
1. Safety
The first benefit of employee training is fundamental level safety. Manufacturing training guarantees that employees understand how to perform the important duties of their job in a safe manner. This not only keeps the employees safe in the workplace, but it also protects their coworkers.
Mandatory industry norms are a good place to start, but you can take it a step further by mandating training on particular equipments and/or the corporate culture. Every good machine shop has safety as its primary tenet. Keeping an eye on the bare necessities of safety is a good idea. Besides, immersive learning technologies, such as virtual reality (VR) or augmented reality (AR), factory personnel should be placed in a learning environment where they may practice operating and fixing equipment without risking their safety. This ensures they are prepared for the real task and can carry out processes with confidence when the time comes.
2. Efficiency
Training enables employees to experience new methods and skills that they can utilize to develop more efficient ways to complete tasks. Furthermore, the rapid growth of the industry means that new equipments and processes will be frequently introduced. A mandatory manufacturing training will facilitate staff’s capabilities to comfortably handle those new equipments and processes. As their proficiency increases, so does their productivity. Training reduces waste and errors, which can both indirectly and directly add to the customer experience. And every employee, regardless of skill level or previous experience, can always benefit from diversified training.
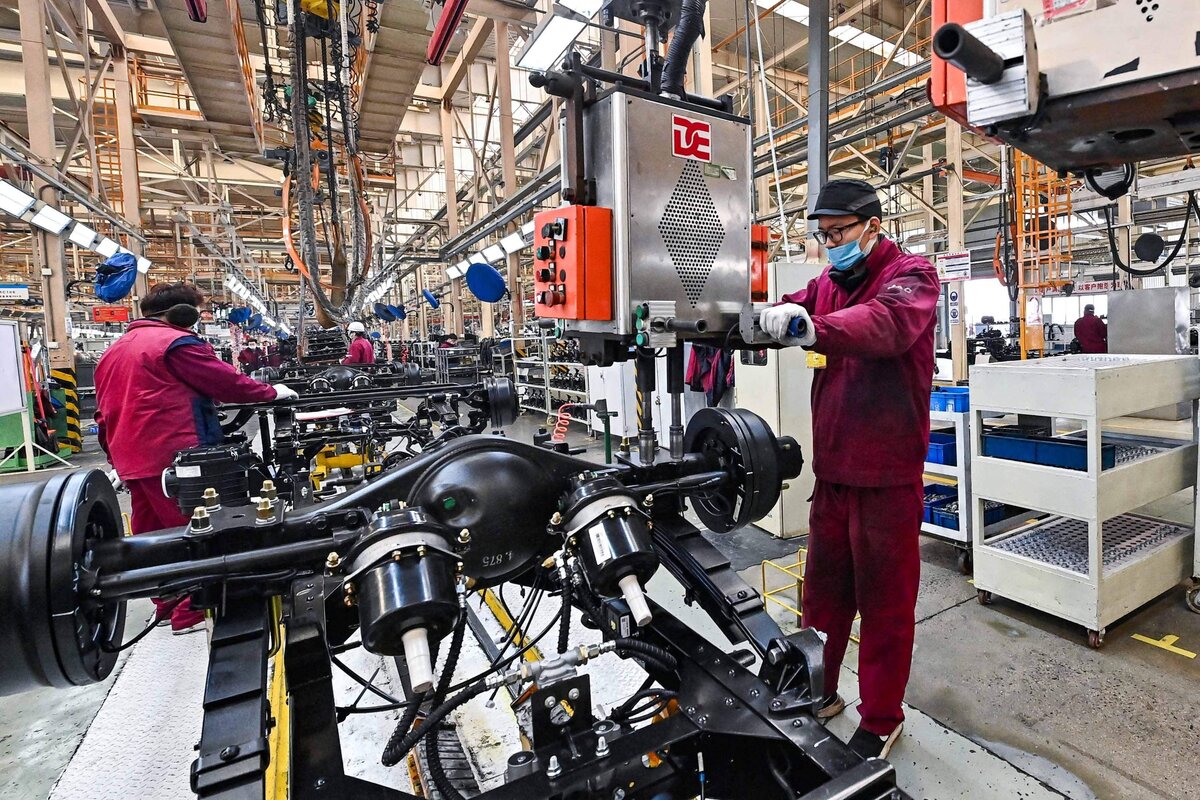
3. Operational flexibility
Cross-training should be a part of the training regimen as corporations need to be ready for the unexpected. Specifically, when a key employee falls sick or needs a leave of absence, cross-trained employees will be able to help the business to continue functioning smoothly. Cross-training can be done whenever, even during vacations or peak times. Therefore, this reduces production downtime and high costs associated with recruiting and training new employees or temporary workers.
In the case of a breakdown, projects and workers may be relocated to other equipment easily thanks to cross-training. Your manufacturing company’s general work environment will benefit as a result, and this might have a positive impact on profits. Additionally, during high-demand situations, companies that conduct cross-training have a better chance of recovering quickly from major disruptions thanks to the flexibility of their staff.
4. Employee retention
Training may minimize turnover by enhancing staff retention and work satisfaction. Employees will be more inclined to stay with a company that promotes their growth through training and growth opportunities. Training programs that begin on Day 1 and continue throughout an employee’s lifecycle aid in the development of long-term workers who support the success of your firm. Organizations that have a lower turnover rate not only save money but also develop a more experienced workforce.
Production training also facilitates the development of a culture of continuous improvement within the enterprise. Employees feel they are an integral part, contributing to the development of the business. More importantly, they feel empowered to make suggestions that help improve the company’s operations. All these factors create an environment that supports each individual’s career growth, thereby building their loyalty to the business.
Typical topics covered during manufacturing training
- Onboarding: Support your employees to succeed in their roles by introducing them to their company and outlining their mission.
- Equipment knowledge: Guarantee that your personnel understands how to operate and maintain equipment in a safe and precise manner.
- Process training: Guide complex processes and conduct hands-on training to maximize employee productivity.
- Safety Guidelines: Educate employees on safety practices while working and develop a team of proactive safety advocates.
Manufacturing training covers a variety of topics to prepare employees for work, thereby driving a business’s innovation and growth. When it comes to investing in employee training and upskilling, companies should focus on developing proper training programs that fit with the company’s culture and development strategy, which ultimately leads to improved outcomes.
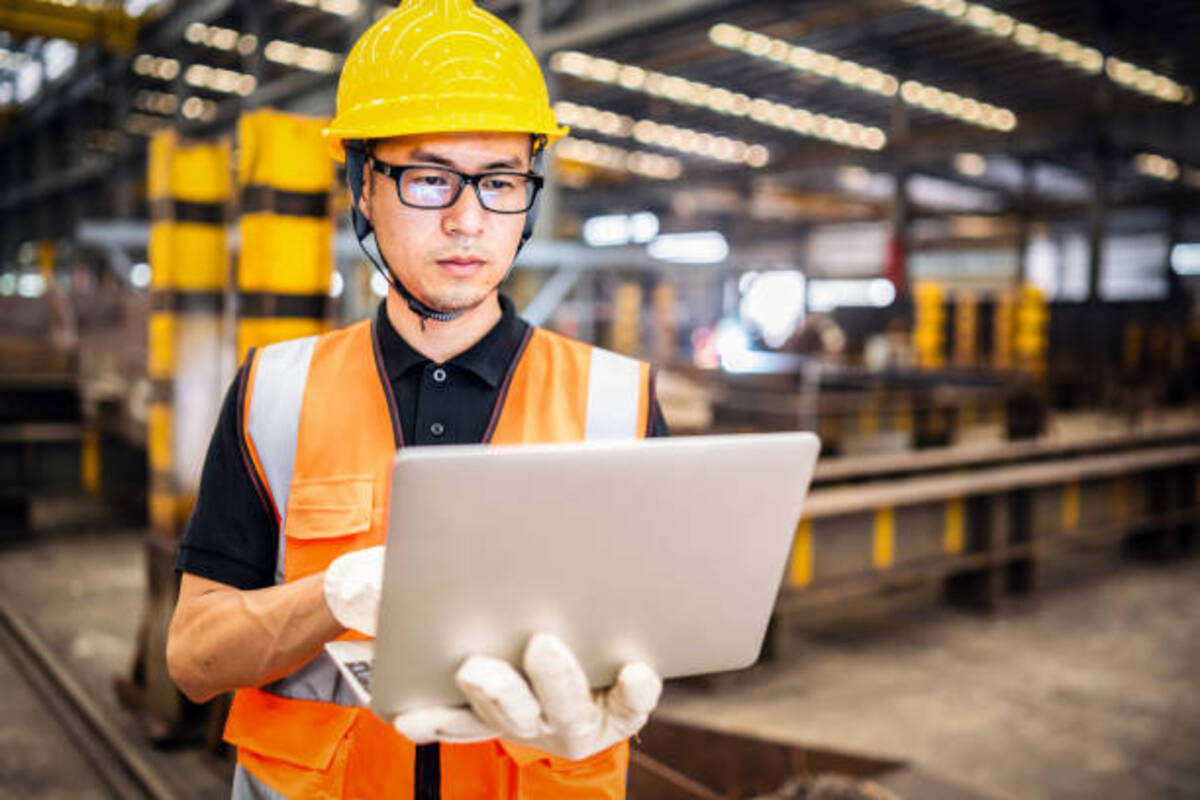
However, before moving to the technical part of manufacturing training, employees need to be equipped with basic skills to grasp the training thoroughly. Nowadays, most technical documents are written in English. Therefore, the preparation of this language skills for employees is a must.
There are various ways to deploy an English training program for your staff, one of which is by using a third-party system rather than building your own. It can save a lot of time and effort by just finding the right learning method for your employees instead of building your own one. A popular example of English learning software is English speaking application ELSA Speak. The application is equipped with AI technology to analyze the user’s voice to detect errors and correct them quickly. In addition, the lessons of ELSA Speak are also customized based on the learner’s level and the business field of the enterprise so that learners can apply the lessons to their daily work environment. Moreover, ELSA Speak is an “L&D assistant” for employers as it can provide reports on employee learning progress, to help measure investment efficiency.
It can be seen that a comprehensive, well-designed training program along with basic skills like English fluency provides numerous advantages to firms. It supplies employees with the skills they need to operate intricate machinery and efficiently complete complex processes. Hence, helping workers to stay safe and well-being during work, eventually contributes to the overall development of the company.
Also you can explore more about our training solution for manufacturing businesses
here.
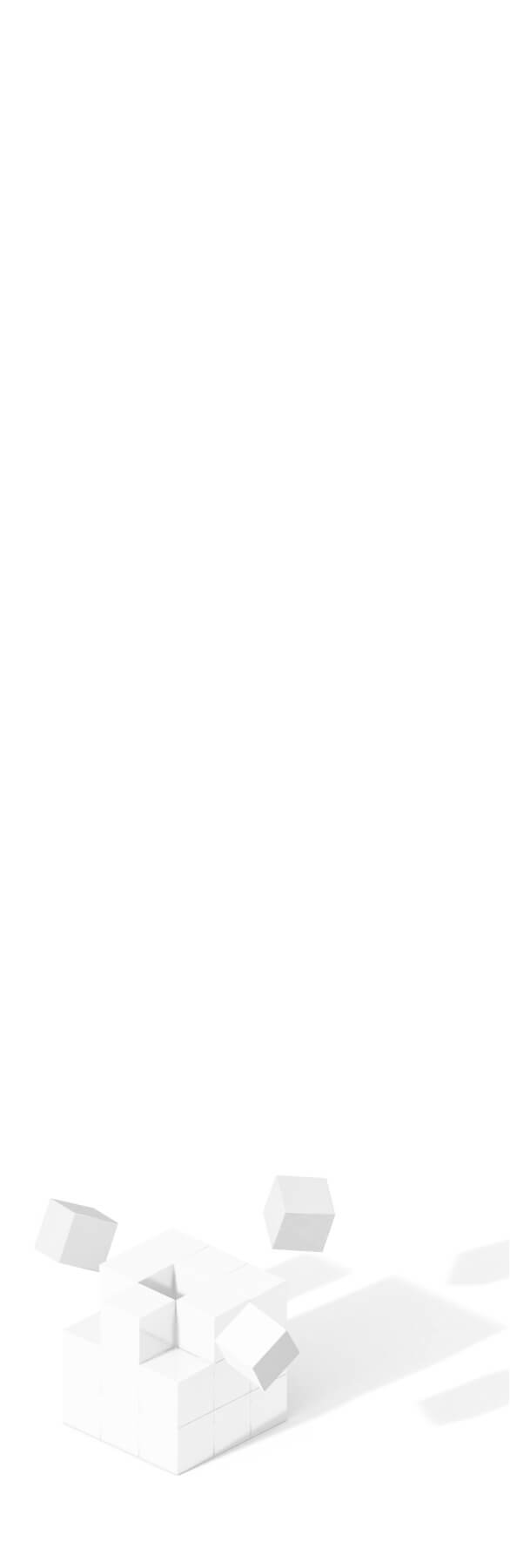