Key Workforce Challenges In Manufacturing - Talentnet survey report
Key Workforce Challenges In Manufacturing - Talentnet survey report
February 7, 2025
Manufacturing executives face a critical inflection point in management. The convergence of technological transformation, demographic shifts, and evolving worker expectations creates unprecedented workforce challenges manufacturing companies must address. These forces reshape traditional employment models and demand immediate strategic response. Companies that fail to adapt risk losing competitive position in an increasingly dynamic market.
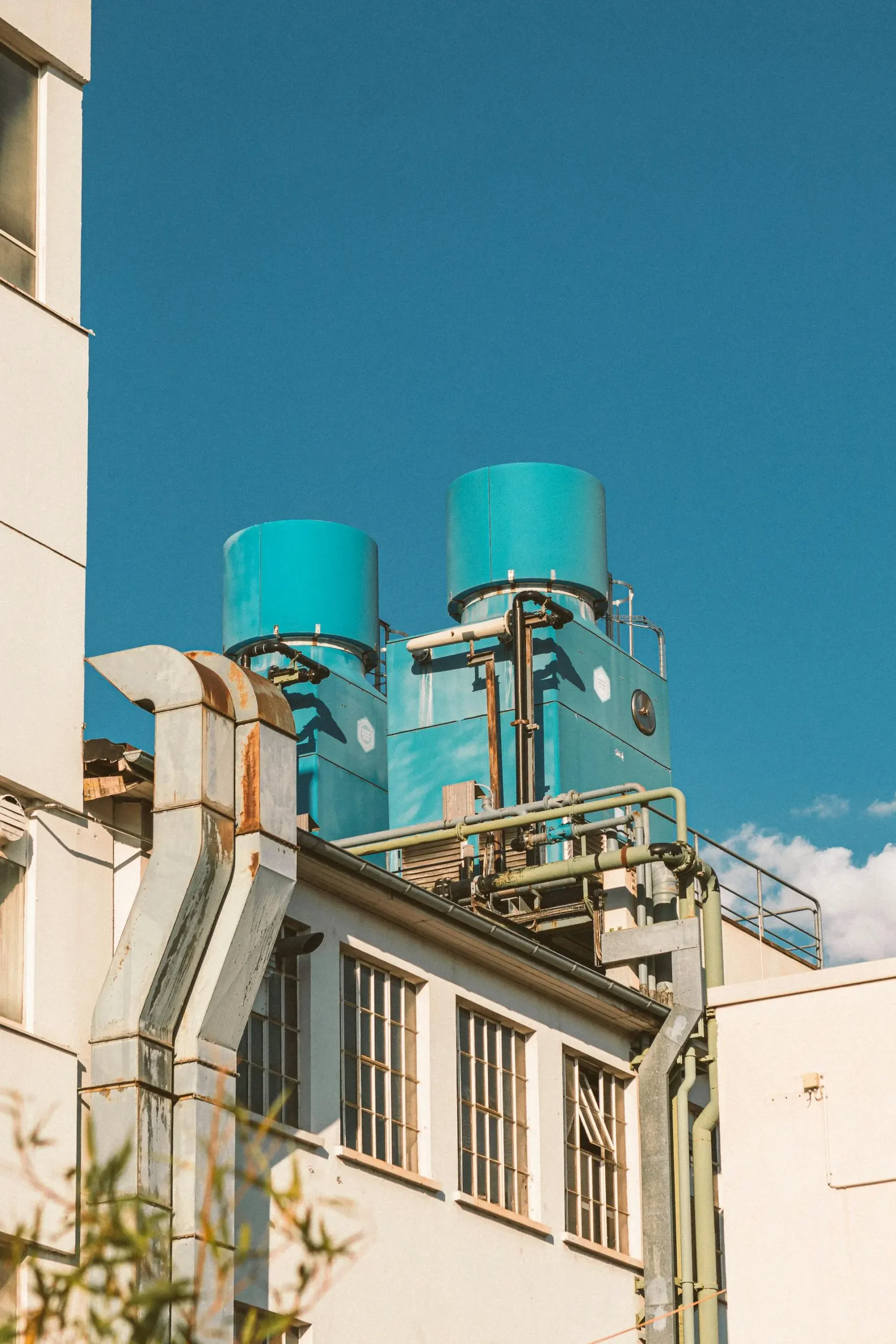
Current manufacturing workforce trends indicate that talent acquisition strategies from five years ago no longer deliver results. These dynamics demand a fundamental shift in human capital management. Companies must navigate complex challenges to remain competitive. These challenges are multifaceted, impacting both Foreign Direct Investment (FDI) and local/joint-venture companies. CEOs and business leaders need to understand these dynamics. Manufacturing leaders must rethink their talent value proposition.
Key Challenges for FDI Companies
Manufacturing FDI companies face unprecedented workforce pressures that threaten operational stability and growth targets.
1. Employee Retention and Engagement
According to the Talentnet survey, 65% of FDI companies stated that employee retention and engagement remain significant challenges for manufacturing companies.
Employee disengagement is costing manufacturers heavily. The Manufacturing Institute’s 2024 Engagement Study shows only 25% of manufacturing employees are actively engaged. This low engagement leads to 81% higher absenteeism and 41% more quality defects.
These engagement issues create a significant financial burden for manufacturers. Direct replacement costs average $50,000 per voluntary departure, while disengaged workers reduce overall productivity by 23%.
The root cause stems from changing workforce expectations. It is identified that 83% of workers prioritize job satisfaction, while 69% value family-oriented cultures and work-life balance. This shift in worker priorities conflicts with traditional manufacturing environments, creating a fundamental mismatch between employee expectations and workplace realities.
On the other hand, engaged workers have 70% lower turnover rates and achieve 44% higher profitability than non-engaged workers, establishing a clear link between engagement and business performance. Retaining a highly motivated and dedicated workforce is crucial, and this is best achieved by ensuring job satisfaction and offering ample opportunities for professional development and personal growth. By fostering a supportive environment where employees feel valued and see clear career progression, companies can strengthen engagement and reduce turnover, ultimately enhancing long-term workforce stability.
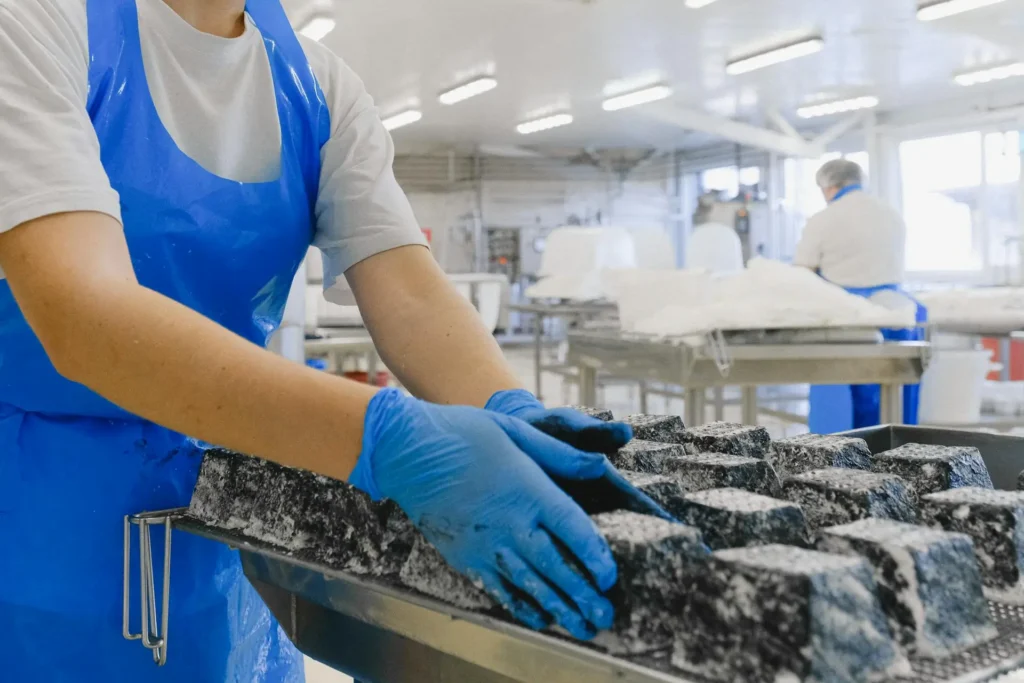
2. Shortage of Skilled Workers (45%)
45% of FDI companies identify a shortage of skilled workers as a major challenge in 2024 Talentnet’s survey report. In today’s rapidly evolving business landscape, there is a significant gap between the demand for and the supply of workers with advanced technical competencies.
This widening skills gap threatens production capacity and innovation potential and is projected to leave 2.1 million positions unfilled by 2030, creating significant operational risks.
Demographics worsen this challenge. The Bureau of Labor Statistics data shows 30% of the manufacturing workforce is over 55. This creates an urgent succession planning need. The Manufacturing Institute confirms that demand for STEM and technical skills outpaces supply, with 75% of manufacturers struggling to attract talent.
This shortage highlights the need for FDI companies to establish strategic partnerships with educational institutions and implement specialized training programs. These initiatives are essential not only for attracting qualified talent but also for equipping them with the necessary skills to meet the industry’s specific demands.
3. Lack of Access to Training and Reskilling Programs (39%)
According to the Talentnet report, 39% of FDI companies cite a lack of access to training and reskilling programs as another major challenge in 2025.
As industries undergo rapid transformation driven by new technologies and evolving processes, The World Economic Forum projects that 50% of manufacturing roles will require new tech skills by 2025, yet 59% of manufacturers lack structured reskilling programs.
This underscores the critical need for organizations to invest in comprehensive training programs to mitigate turnover, boost productivity, and address the looming talent shortages. By fostering a culture of continuous learning, companies can ensure a highly skilled and agile workforce capable of meeting the demands of an increasingly dynamic economic landscape.
Local & Joint-Venture Companies
Local and joint-venture companies face many of the same workforce challenges as FDI companies. They also navigate unique obstacles related to local market dynamics and resource constraints.
1. Employee Retention and Engagement
According to the Talentnet report, similar to FDI companies, 64% of local and joint-venture firms also report their challenges in employee retention and engagement. The financial impact of a disengaged workforce hits local firms harder than their FDI counterparts. Local manufacturers face higher turnover costs due to weaker brand equity.
Career development also shows a critical gap between local and FDI firms. While 75% of employees stay longer with companies offering internal promotions, only 29% of local manufacturers have formal career pathways. This compares poorly to the 45% implementation rate in FDI companies. The disparity creates a competitive disadvantage in talent retention.
To bridge this gap, local manufacturers must invest in structured career development programs that provide employees with clear growth opportunities. Implementing mentorship initiatives, leadership training, and skill enhancement workshops can help create a more engaged and loyal workforce. Additionally, strengthening employer branding through employee recognition programs and competitive compensation packages can improve retention rates.
Furthermore, improving work-life balance through flexible policies, wellness programs, and enhanced benefits can make local firms more attractive to skilled talent. As workforce expectations evolve, companies that proactively address these challenges will be better positioned to retain top employees, reduce turnover costs, and compete effectively in an increasingly dynamic labor market.
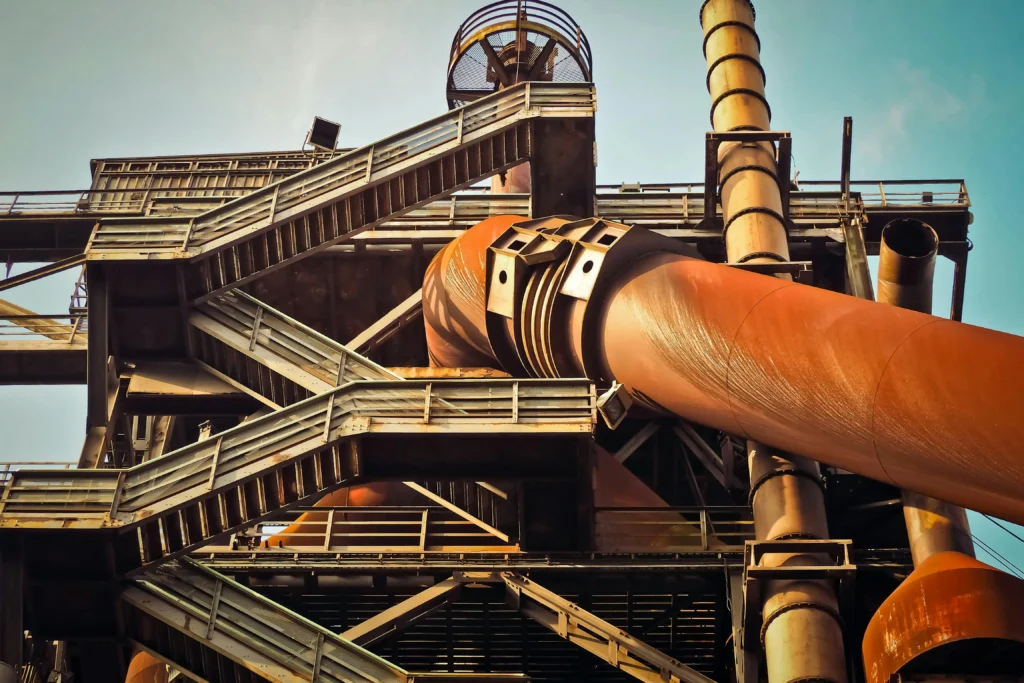
2. Shortage of Skilled Workers
Further in the Talentnet report, 46% of local companies identify the shortage of skilled workers as a persistent challenge in the labor market. The growing demand for specialized technical expertise continues to outpace supply, particularly in manufacturing and high-tech industries. This is a broader issue in the current labor market. By 2030, Vietnam’s manufacturing sector faces a potential crisis with 2.1 million jobs unfilled. Local firms experience 20% longer hiring cycles for technical roles compared to FDI competitors.
This talent shortage is exacerbated by demographic shifts and market competition. Vietnam is one of the fastest-aging countries in Asia, with 25% of its workforce over the age of 55, as reported by the International Labour Organization (ILO). This aging workforce accelerates knowledge loss, particularly affecting local firms that struggle to compete with better-resourced foreign direct investment (FDI) companies for scarce technical talent.
To address this issue, businesses are increasingly looking toward long-term solutions such as forming strategic partnerships with universities and vocational institutions to align curricula with industry needs. Internship and apprenticeship programs have also gained traction as effective ways to nurture talent early and create a pipeline of skilled workers. Additionally, investing in upskilling and reskilling initiatives ensures that existing employees can adapt to evolving job requirements, reducing dependency on external hiring.
By prioritizing these approaches, companies can not only mitigate the skilled labor shortage but also enhance employee retention, strengthen workforce capabilities, and drive sustainable business growth in an increasingly competitive market.
3. Generational Shifts in the Workforce (46%)
By 2025, one-third of Vietnam’s workforce will be Gen Z. However, 70% avoid manufacturing roles despite the sector’s 40% GDP contribution. This in turn becomes a major challenge for 46% of local firms, regarding generational shifts in the workforce according to Talentnet report. As Baby Boomers retire and Millennials and Gen Z become a larger proportion of the employee base, organizations must adapt to the distinct expectations, preferences, and work styles of these different generations. This requires a multi-faceted approach, including:
- Flexible work arrangements: Offering options like remote work, flexible hours, and compressed workweeks can cater to the preferences of younger generations who often prioritize work-life balance.
- Technology integration: Leveraging technology to facilitate collaboration, communication, and knowledge sharing is crucial for engaging tech-savvy Millennials and Gen Z employees.
- Inclusive culture: Creating a workplace that values diversity, promotes open communication, and fosters a sense of belonging is essential for attracting and retaining talent from all generations.
By understanding and addressing the unique needs and motivations of each generation, local firms can optimize team dynamics, improve employee engagement, and enhance overall organizational performance.
Workforce challenges in manufacturing demand comprehensive strategic responses from business leaders. Both FDI and local companies must prioritize employee engagement, address skilled worker shortages, enhance training programs, and manage generational transitions. Companies that implement proactive workforce strategies gain sustainable competitive advantages in operational efficiency and market responsiveness.
Success requires strategic workforce planning and targeted talent solutions. Our Executive Search & Selection service helps manufacturing leaders identify and secure key talent in this competitive market. Through Contingency Search, we provide flexible recruitment solutions aligned with your specific needs and timeline.
The path forward requires decisive action. Manufacturing leaders who effectively address these workforce challenges position their organizations for sustained growth and market leadership in an evolving industrial landscape.
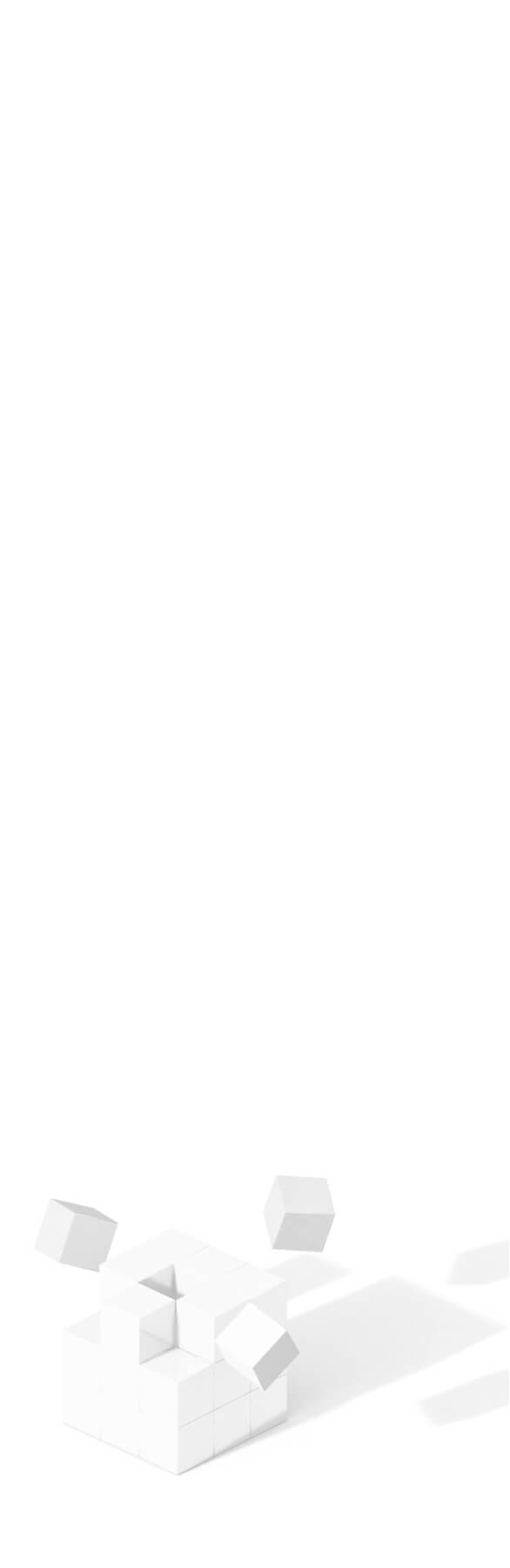